Comprehensive Guide to Pipeline Welding Assessment: Ensuring Honesty and Safety in Pipeline Building And Construction and Maintenance
The stability and safety and security of pipelines are critical in today's facilities landscape, underscoring the important function of welding inspection in pipeline construction and upkeep. Pipeline Welding Inspection. The complexities involved in welding examination raising relevant questions regarding market criteria and the advancing modern technologies that might redefine these techniques.

Significance of Welding Evaluation
Welding evaluation plays an essential function in ensuring the stability and safety of pipeline systems. It works as a fundamental procedure that confirms the top quality and integrity of bonded joints, which are usually one of the most weak spots in pipe building. Through organized assessment, assessors can determine prospective problems such as fractures, porosity, and insufficient blend, which might jeopardize the architectural honesty of the pipeline.
The value of welding evaluation extends beyond simple conformity with market requirements; it likewise safeguards public health and wellness and the atmosphere. Pipelines lugging harmful materials pose substantial risks if failings happen. Effective inspection procedures help prevent leaks and tears, minimizing ecological damage and securing communities. Moreover, extensive examinations can enhance the long life of pipeline systems, minimizing the requirement for costly repair services and downtime.
In enhancement to guaranteeing safety and compliance, welding inspection promotes a culture of high quality guarantee within organizations. By prioritizing examination throughout the welding process, business can construct a credibility for integrity and excellence, inevitably resulting in boosted client self-confidence and business opportunities (Pipeline Welding Inspection). Therefore, the value of welding evaluation can not be overemphasized in the context of pipe building and construction and upkeep
Secret Welding Procedures
Various welding processes are employed in pipe building and construction, each with its own advantages and applications. Among one of the most widely utilized methods are Protected Steel Arc Welding (SMAW), Gas Tungsten Arc Welding (GTAW), and Gas Steel Arc Welding (GMAW) SMAW is favored for its flexibility and ability to carry out well in various environmental conditions, making it ideal for area applications.
GTAW, usually described as Tungsten Inert Gas (TIG) welding, is identified for its capacity to generate high-quality welds with excellent control over heat input, making it ideal for thin-walled pipes and stainless steel products. GMAW, or Steel Inert Gas (MIG) welding, uses high deposition rates and is efficient for large-scale jobs, commonly used in the construction of pipelines in controlled atmospheres.
In Addition, Immersed Arc Welding (SAW) is utilized for its deep penetration and high productivity, specifically in the building of large-diameter pipes. Each of these procedures adds to the total integrity and security of pipeline buildings, allowing welders to pick one of the most suitable method based upon product type, task demands, and ecological conditions. Understanding these vital welding procedures is essential for reliable pipeline welding inspection.
Common Defects and Their Influence
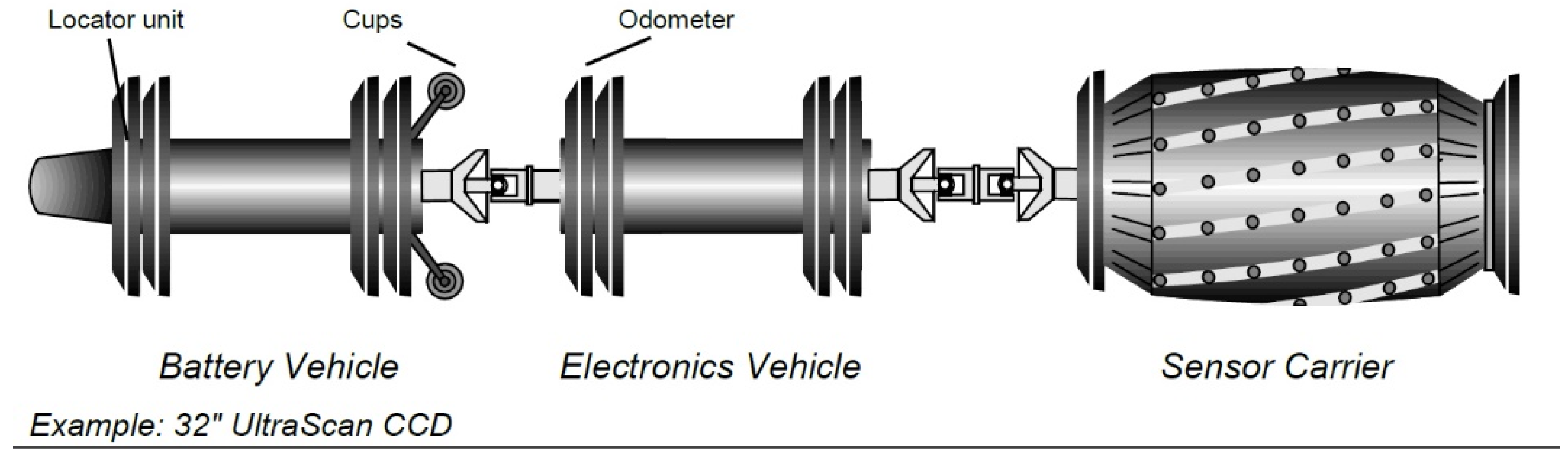
Porosity, identified by tiny gas pockets entraped within the weld, deteriorates the material and can cause leaks. Splits, which might take place due to thermal stresses or improper air conditioning, can circulate and result in structural failing under stress. Damaging, where the base metal is deteriorated along the weld grain, minimizes the effective cross-section of the pipe, enhancing the risk of crack.
Incomplete blend happens when the weld steel does not properly bond with the base steel, causing weak areas that might fall short under stress. Slag inclusion, the entrapment of non-metallic material within the weld, can likewise deteriorate the joint's integrity. Recognizing and addressing these flaws early in the building and construction procedure is critical to making sure the long-term integrity and safety of pipeline systems, thereby safeguarding both the framework and the environment.
Examination Methods and Devices
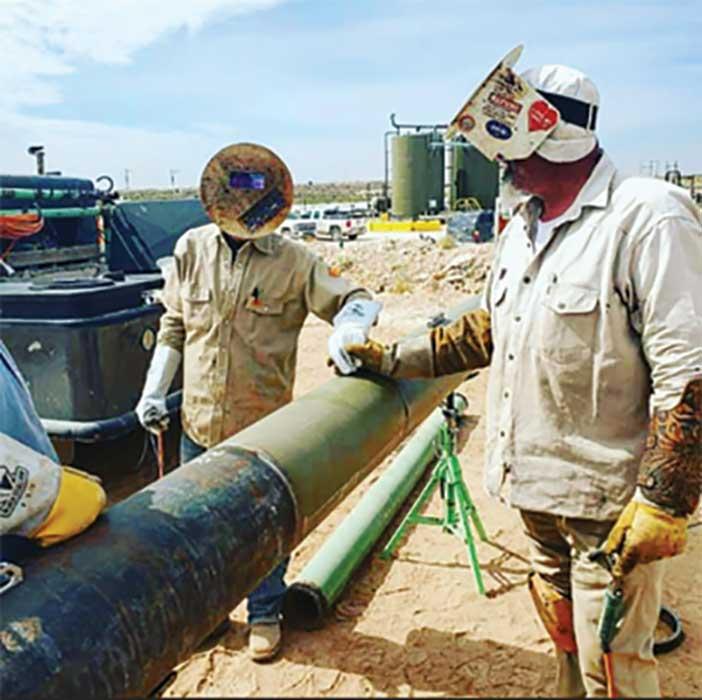
Aesthetic assessment is the first line of protection, allowing examiners to identify surface area irregularities, imbalance, or other noticeable defects. Ultrasonic testing employs high-frequency sound waves to find inner flaws, providing exact depth measurements and defining flaws without harming the weld. Radiographic screening utilizes X-rays or gamma rays to create photos of the weld, allowing the recognition of internal spaces, fractures, or inclusions.
Magnetic fragment screening is especially reliable for discovering surface area and near-surface stoppages in ferromagnetic materials. This method entails applying an electromagnetic field and fine iron bits to the weld, exposing defects through the accumulation of fragments at defect websites.
In enhancement to these techniques, specialized tools such as automated ultrasonic screening equipment and digital radiography systems boost evaluation precision and performance, guaranteeing a thorough assessment of pipe welds throughout building and construction and maintenance.
Ideal Practices for Compliance
Sticking to best practices for compliance in pipe welding evaluation is critical for ensuring the integrity and safety of the facilities. Organizations has to develop a detailed high quality administration system that straightens with industry standards such as ASME, API, and AWS. This includes developing comprehensive welding procedures that specify the materials, techniques, and credentials required for welders.
Routine training and qualification of examination employees are vital to maintain high expertise degrees. Assessors must recognize with various non-destructive testing (NDT) methods, including ultrasonic screening, radiographic screening, and visual evaluation, to successfully identify potential issues.
Paperwork plays an important function in compliance; maintaining exact records of evaluations, weld treatments, and personnel credentials assists to ensure traceability and liability. Arranged audits and reviews of welding practices need to be carried out to identify locations for improvement and make sure adherence to established procedures.
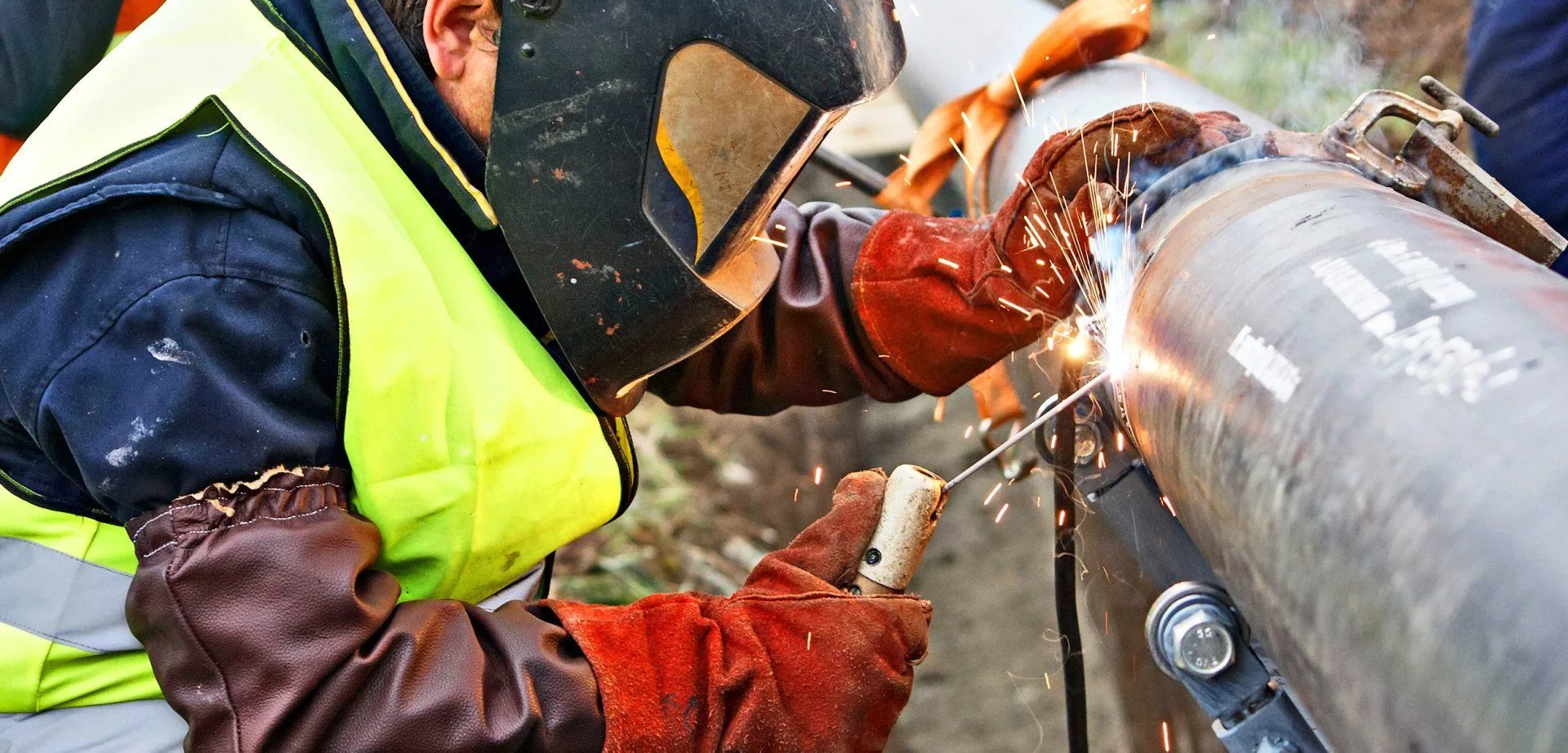
Verdict
In final thought, the implementation of extensive welding inspection procedures is paramount for ensuring the honesty and safety of pipe construction and maintenance. Continual improvement in assessment processes will certainly add to the longevity and dependability of pipe systems, emphasizing the vital duty of welding evaluation in the market.
The honesty and safety of pipelines are extremely important in today's facilities landscape, highlighting the crucial duty of welding inspection in pipe construction and upkeep. Recognizing these linked here key welding processes is vital for reliable pipeline welding evaluation.
Adhering to finest practices for compliance in pipe welding examination is essential for making sure the honesty and safety and security of the infrastructure.In verdict, the implementation of strenuous welding evaluation procedures is extremely important for making certain the honesty and safety and security of pipeline construction and upkeep. Constant enhancement in assessment procedures will contribute to the longevity and reliability of pipe systems, emphasizing the crucial role of welding evaluation in the industry.
Comments on “Comprehensive Pipeline Welding Inspection: Protecting Infrastructure Integrity”